Atomised Mist: Our Latest Innovation on Dust Suppression
Silica dust, along with other crushing-related dust, is not only an eyesore for the local community and damaging to plant and equipment but, most importantly, poses a risk to workers’ health. We can’t eliminate it so we need to control it.
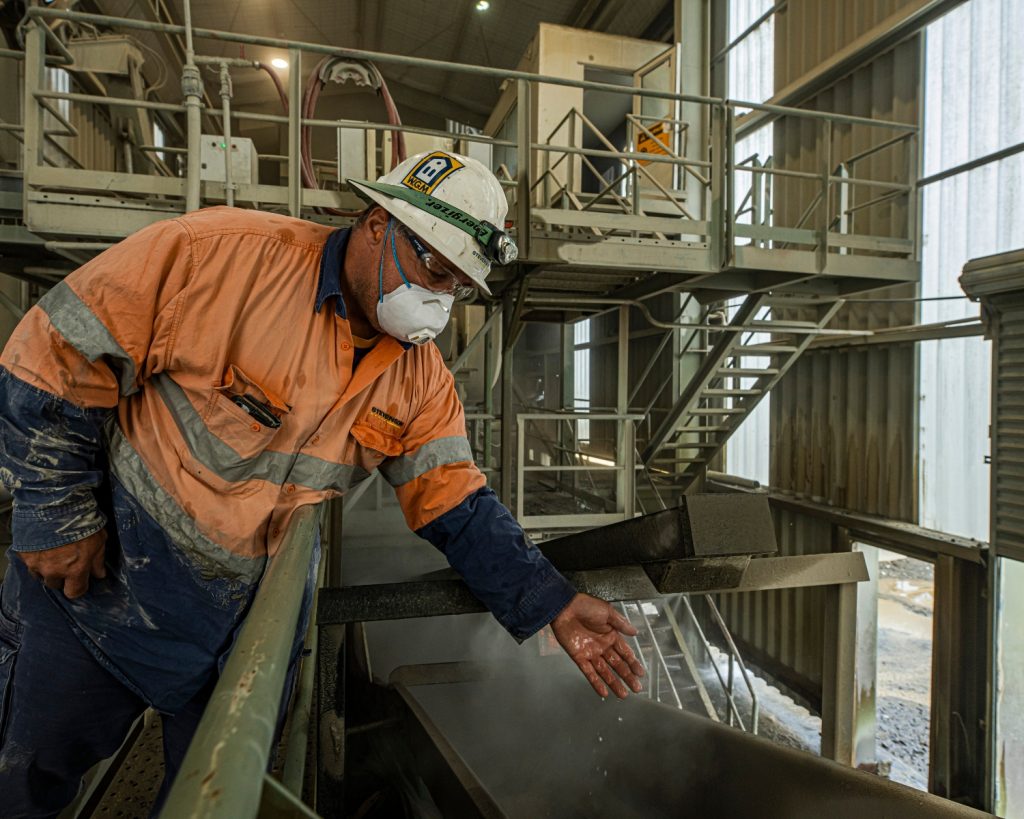
The dust we were concerned about is much finer than a human hair, invisible to the naked eye, and poses a serious risk of long-term lung damage.
To address the issue, the Stevenson engineering team collaborated with Peter Schierhout from Spraying Systems to design an innovative dust suppression system. Traditionally, water spray bars are used for dust suppression, but they come with several challenges.
Excessive water can wash fines away from the product, large droplet sizes can fail to capture airborne dust efficiently, and excessive water use leads to drenched equipment and wastage. Dust extraction is also an option, but it requires a captured system, which is not always effective given the size of the crushers and the nature of the crushing process. While these traditional systems can work, they are neither efficient nor sustainable.

Collaborating closely with the team from Spraying Systems and exploring a multitude of solutions—such as atomising nozzles and ultra-fine high pressure nozzles— we developed a solution tailored to the main areas of dust generation. This solution combines water spray with compressed air. By atomising the water droplets into a fine mist, they remain suspended in the air long enough to capture airborne dust particles. Once the water droplets attach to the dust, the particles become heavy enough to drop onto the conveyor. The engineering and maintenance teams then designed systems for the primary and tertiary plants at Drury.
“…the system uses only 6 litres of process water per hour per nozzle, combined with compressed air at 4.2 bar to create the fine mist—compared to the previous use of 900 litres per hour...”
Since September 2023, Stevenson has been implementing these dust suppression measures across the site. At the primary plant, the new atomising nozzles (fig 4) were installed under the jaw crusher and on the CV08B conveyor (Photo 1), reducing dust by an impressive 90% and water usage by an incredible 97%. The system uses only 6 litres of process water per hour per nozzle, combined with compressed air at 4.2 bar to create the fine mist—compared to the previous use of 900 litres per hour.
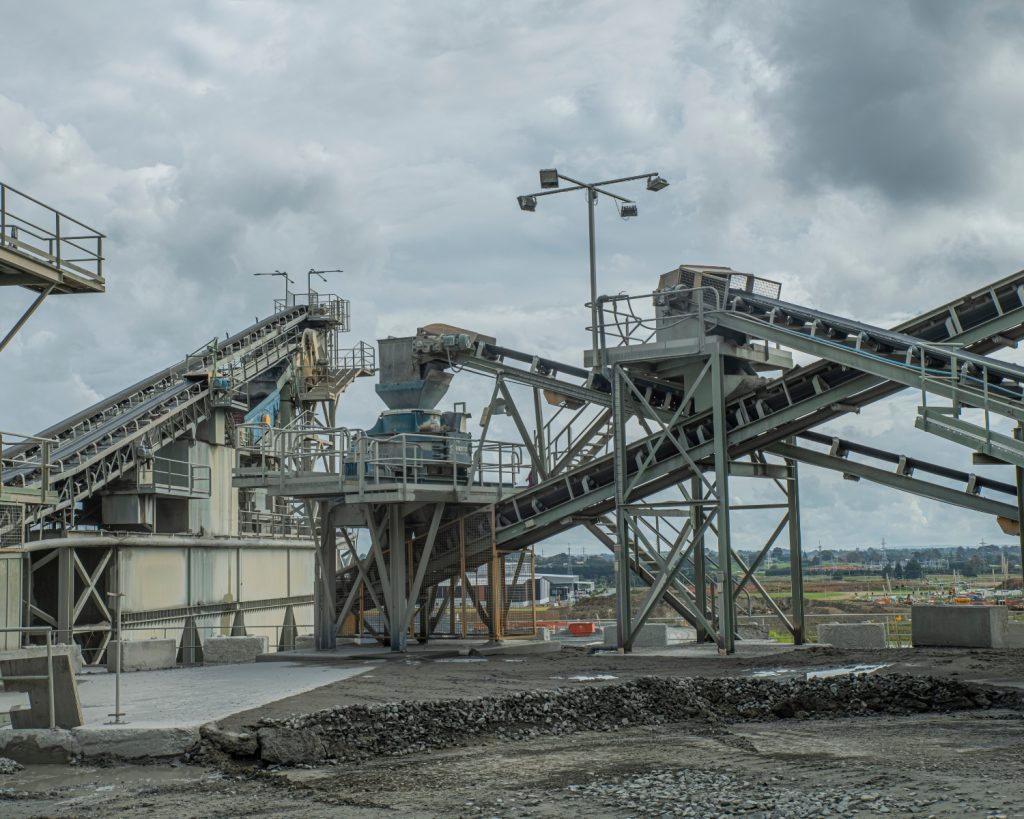
Simultaneously, a digital upgrade was carried out, relocating the operator from the Primary plant control room—previously exposed to dust and noise—to another control room, providing a safer and quieter environment. At the tertiary plant, the Barmac 9100 crusher was enclosed, capturing dust, and directing it to an extraction system, which has reduced dust exposure by nearly 100%. Ongoing projects include covering conveyors to eliminate dust dispersal from the 8100 Barmac and installing a cover on the ballast belt infeed chute, both of which will direct dust into the existing extraction system.
These innovations will drastically reduce airborne dust and the associated risks, as well as significantly decrease water usage. Adam emphasises the importance of these initiatives: “With dust regulations tightening across New Zealand, it’s essential to keep dust levels low for compliance and to protect the health of our workers. Our dust suppression solutions ensure staff are not exposed to harmful silica dust, creating a safer work environment for everyone.”
“These innovations will drastically reduce airborne dust and the associated risks, as well as significantly decrease water usage. “
This comprehensive dust management project is just the beginning, with plans to extend these innovative solutions to other areas, including the asphalt and sealed chip plants, and across our wider business.