Harnessing Perlite
Stevenson has been working with the natural volcanic material perlite to create a concrete product with a dramatically reduced carbon impact.
The carbon footprint for perlite is under 100 kg per tonne, much less than the 500-800 kg produced for each tonne of cement and lower than other supplementary cementitious materials – SCMs – like fly-ash or slag.
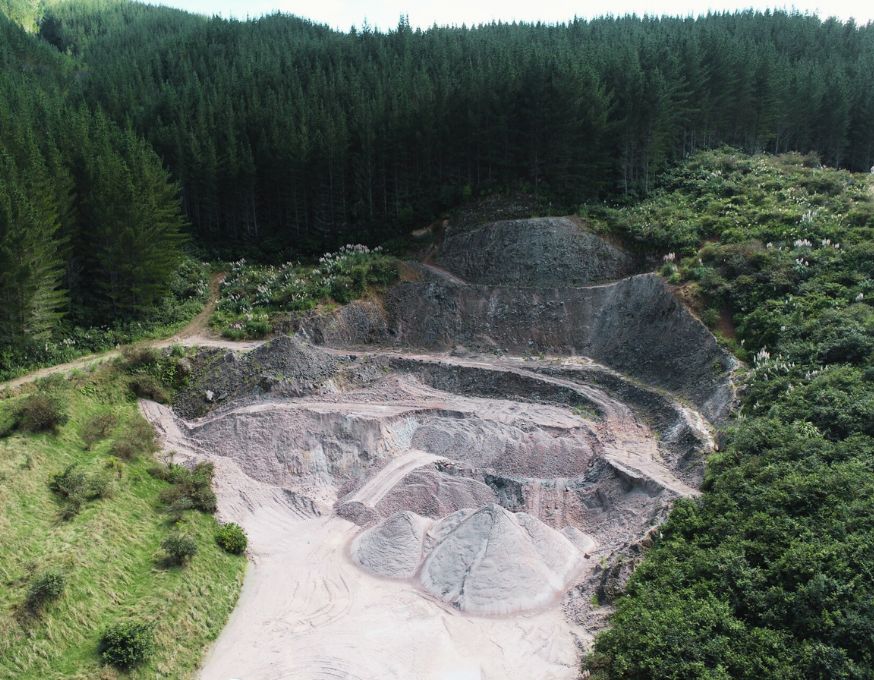
It also has the benefit of being a natural New Zealand product, yet still able to be used in conjunction with other SCMs to further reduce carbon content, business development manager Maria Baker says.
“Whilst we are happy to use fly-ash and slag, and we can use them together, our product is definitely superior because you can’t beat its carbon content and the fact it’s a natural New Zealand product that isn’t a waste stream of high carbon industries such as steelmaking or coal burning.”
The company’s goal is to release the newly trademarked Eco-Perlite concrete product by May, after some further trials to ensure it has the correct consistency.
It plans to initially include only low amounts, replacing up to 5 per cent of cement with perlite. Once the company has enough of its own data, the proportion of perlite will gradually be increased – ideally to up to 30 per cent.
Characteristics
Perlite is a type of pozzolan which ordinarily has little or no cementitious characteristics.
But when the material is finely ground and added to water, it reacts with calcium hydroxide at normal temperatures to form new compounds.
HR Cement, Holcim, and Golden Bay Cement have also been exploring the use of SCMs to produce lower-emission cement.
Recent start-up Neocrete received funding from Waka Kotahi’s innovation fund to trial low-carbon concrete mixes using pozzolans.
ConcreteNZ’s net zero carbon roadmap to 2050 – released last year – notes the vital role of SCMs such as pozzolans in reducing the carbon footprint of concrete.
It notes that NZ has an abundance of natural pozzolans, but further research and development is required to commercialise them at scale.
Extraction
The pozzolan is extracted from the company’s quarry near Tokoroa – pictured – then transported to Stevenson’s Drury quarry where it is stored under cover, dried and milled.
While perlite is a hard rock, the material is free dug from the quarry and breaks out quite fine.
“You don’t really need too much to crush it, but we use either a jaw or a cone then we screen the oversize to take a 20mm product for our plant,” Baker says.
The quarry is permitted to extract 50,000 tonnes per year. Baker says they will look to build toward those tonnages as perlite is used at higher levels in concrete .
At this point they have a 25 year resource with options to expand further.
“The resource is so important for the industry that Stevenson plan to invest further in such a highly sought after environmentally friendly product.”
Testing
Perlite has been used for decades to lower the carbon content of concrete overseas – frequently at levels up to 30 per cent – giving the company confidence that it will prove a game-changer in NZ as it has overseas.
But before they introduce the product to the market, a further suite of tests needs to be undertaken to account for the finer material which they are now getting out of their plant.
“What we would like to do is get our plant running exactly how we want it and then we will do particle size distribution testing, mortar testing, concrete testing and start building up our data set.”
An independent laboratory in Australia will also undertake concrete testing and more extensive analysis of the product.
“Once we get our data back from there, we will continue to improve the product and make sure that it’s suitable at higher percentages.”
Strength testing
For the time being, Baker says the product using 5 per cent perlite has no impact on the quality of concrete except lowering the carbon.
The 5 per cent perlite product has similar strengths as standard concrete when measured after one, three, seven or 28 days.
The company’s challenge next is to obtain that early strength in concrete containing higher proportions of perlite so that it can be used as structural concrete.
However, Baker is confident that can be achieved through the use of ad mixtures or different kinds of cement.
“As we build our data set and see what we can achieve, we will be able to increase the amount of perlite we can use in the concrete and further drop down that carbon content.”
Published by Inside Resources, author Heidi Bendikson – Wed, 20 Mar 2024.